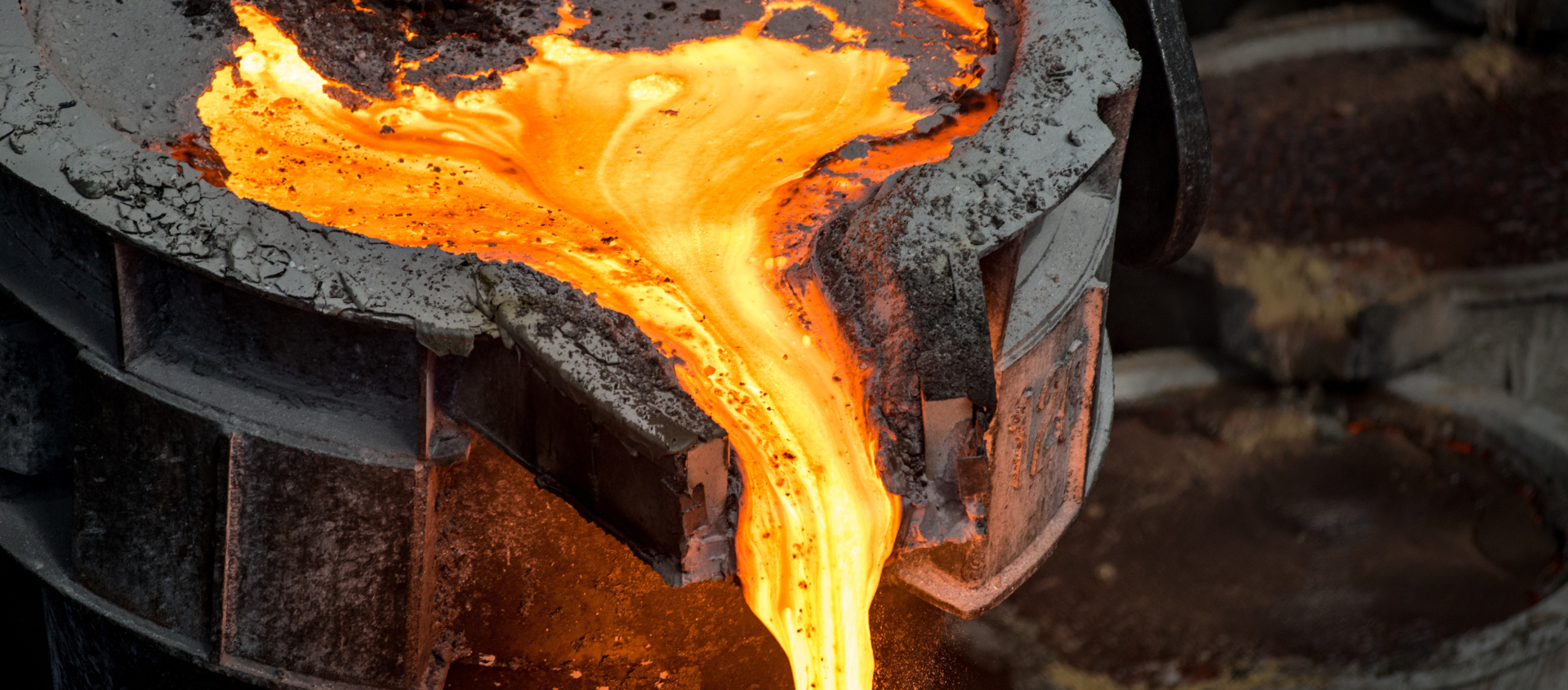
Prodotti per Fonderie Ferrose e Non Ferrose
Cored wire treatments for cast iron into ladle
In the 1980s, the steel foundry industry faced the imperative of enhancing control and automation, while incorporating additives and inoculants to elevate the quality of metallurgical treatment in the Ladle. This period marked a significant turning point for ductile iron and compacted graphite iron foundries, as they recognized the cored wire system as a straightforward, efficient, and expeditious method for magnesium treatments. Notably, this method led to a substantial reduction in material wastage.
The advantages of employing the cored wire system were swiftly grasped by foundries, leading to the development of diverse applications for metallurgical treating ductile irons and compacted graphite irons foundries. Presently, there exist various applications in foundries dedicated to ductile irons and compacted graphite irons production of foundries. Cored wire finds predominant use in spheroidization and inoculation, with less frequent applications in desulphurization and all modification treatments in the Ladle.
This method stands as a testament to continuous advancements in metallurgical processes, contributing significantly to the enhancement of ductile iron foundry practices.

Cored Wire Method
In summary, Duedi's Cored Wire Treatment System is the most economical, advanced, reliable, and ecological approach to treatment processes for the production of ductile iron and compact graphite iron. Moreover, it accommodates various metallurgical processes, including spheroidization, inoculation, and perlitization, making it a versatile and indispensable solution for foundries committed to excellence in ductile irons and compacted graphite irons production.
For further information, stay connected by following updates on this website about the latest advancements in this cutting-edge DUEDI’s Cored Wire Treatments technology.
UNIFORMITY OF THE MELT:
The System ensures the uniformity of the melt by facilitating the Magnesium reaction at the bottom of the treatment ladle, thus guaranteeing a homogeneous melt throughout the entire treatment cycle.
01CONTROLLED QUANTITY OF INSERTED ALLOY:
The quantity of alloy inserted into liquid iron remains constant, providing precise control over the cored wire introduced during each treatment into the ladle.
02MONITORING CAPABILITIES:
The integrated automation in Duedi’s Cored Wire Treatment System allows for the monitoring of each treatment cycle. This involves the injection of cored wire through the sturdy machine named feeder or injector managed by dedicated and customized hardware + software inside an electrical panel.
03ENVIRONMENTAL IMPACT MINIMIZATION:
The System minimizes the impact of fumes generated during any transformation phase through the implementation of a special and customized indirect fumes extraction hood.
04EXTENDED AND DURABLE USE OF EXISTING LADLE:
The Duedi’s Cored Wire Treatment System facilitates the extended use of a single treatment and casting Ladle over time, contributing to operational efficiency.
05
The Duedi’s Cored Wire System is distinguished from previous treatment methods because:
- FOR SPHERONIZATION PROCESSES
Higher efficiency therefore less reagent consumption; a higher degree of cleanliness; highest reproducibility; improved magnesium recovery; Applicability of inert gas shielding; indirect aspiration of treatment smokes; minimal aspiration smoke evolution; lesser temperature losses; reduced temperature loss simulation and sequential addition of inoculation agents; weighing of added various additives is eliminated; precise additions of present elements; low maintenance costs of the single treatment and casting ladle; automation of the treatment System. - FOR INOCULATION PROCESSES
Improvement of working conditions; eliminations of treatment ladle build-up and refractory savings; inter slag; precise additions of the preset elements; lesser temperature losses; low maintenance costs of the single treatment and casting ladle; automation of the treatment system.